工艺分析报告
引言
工艺分析是工业制造和质量控制的核心环节,其目的是通过系统化的检测与评估,确保产品从设计到生产的全流程符合技术标准与性能要求。随着现代工业对精度和可靠性的需求日益提升,工艺分析的科学性和全面性已成为企业竞争力的重要指标。本报告基于实际生产场景,从检测范围、检测项目、检测方法及检测仪器等维度展开论述,为工艺优化和质量提升提供参考依据。
正文
一、检测范围
工艺分析的检测范围需覆盖生产全流程,具体包括以下内容:
- 原材料性能:金属、塑料、复合材料等原材料的物理化学特性;
- 生产过程参数:温度、压力、时间等工艺控制指标的稳定性;
- 成品质量:尺寸精度、表面缺陷、力学性能等核心指标;
- 环境影响:湿度、粉尘、振动等外部因素对工艺的干扰。
二、检测项目
根据工艺特点,检测项目可分为以下类别:
- 物理性能检测:硬度、拉伸强度、抗疲劳性等;
- 化学成分分析:材料元素组成、杂质含量及分布均匀性;
- 表面质量评估:粗糙度、涂层厚度、裂纹与气孔检测;
- 尺寸与几何精度:关键部件的公差、形位偏差等。
三、检测方法
针对不同检测目标,需采用多元化的技术手段:
- 光谱分析法:用于快速测定金属材料的元素成分;
- 金相显微技术:观察材料微观组织结构及缺陷分布;
- 无损检测(NDT):通过超声波或X射线探测内部缺陷;
- 三坐标测量:高精度获取复杂工件的三维尺寸数据。
四、检测仪器
先进仪器设备是工艺分析的技术保障:
- 直读光谱仪:可在30秒内完成金属成分的定性定量分析;
- 显微硬度计:支持维氏、努氏等多种硬度标尺的自动测量;
- 工业CT扫描仪:实现非破坏性的三维内部结构成像;
- 激光跟踪仪:用于大型装配件的动态形变监测,精度达±15μm。
五、数据分析与工艺优化
工艺分析需结合统计过程控制(SPC)方法,通过以下步骤实现持续改进:
- 建立关键指标的过程能力指数(CPK)模型;
- 利用Minitab等工具进行变异源分析;
- 针对异常数据点开展根本原因分析(RCA);
- 制定工艺参数调整方案并验证实施效果。
结论
工艺分析作为现代制造业的基石,其系统化实施能显著降低质量风险并提升生产效率。通过明确检测范围、采用科学的检测方法与仪器、建立数据驱动的优化体系,企业可构建完整的质量闭环。未来,随着工业互联网和人工智能技术的融合,工艺分析将向智能化、实时化方向持续演进,为高端制造注入新的发展动能。
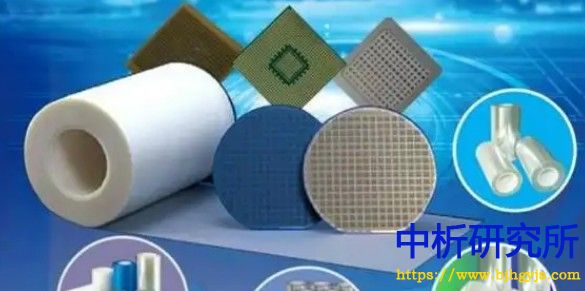
了解中析
实验室仪器
合作客户
